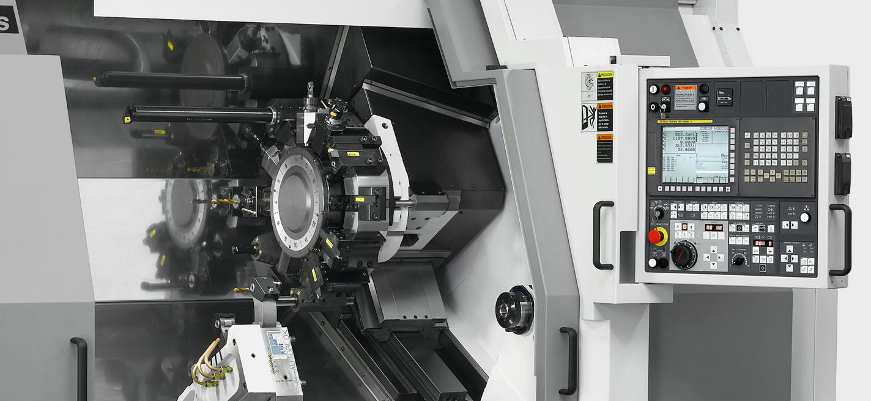
CNC Technology And Metal Processing
CNC (Computer Numeric Control) machines are automated tools that are controlled by programmed commands modeled with a computer that also plays an important role in managing them.
Historic development of the CNC technology
CNC technology began to develop in the 40s and 50s of the last century. The then-known technology of numerical control was based on existing tools and machines used in the processing of materials.
The servomotors that controlled their movements were added to the mentioned. The milestone in the development of the CNC machines, as well as in the change of the production process, is the development of computers and electronics in general.
Such innovations and technology allow you to send program commands from your computer directly to the machine that directly executes them.
The first CNC machine was manufactured in America at the Massachusetts Institute of Technology (M.I.T) and it marked a major milestone in the manufacturing process. Unlike today’s computer-controlled machines, this machine was operated with a drilled paper ribbon. One of the curiosities associated with them is related to the management unit that was larger than the CNC machine. From then on, the CNC technology is progressing and becoming more and more advanced so it is almost impossible to imagine a modern machine park without the CNC.
The advantages of using the CNC technology
Today’s production of metal parts without the use of the CNC technology is unthinkable. The benefits of using the CNC machines are many. Some of them are reflected in the flexibility of the machining process (especially with CNC milling and drilling), precision and (CNC cutting) processing speed.
However, one of the most important and greatest advantages of using the CNC machine in metal processing is the fact that the CNC can perform multiple operations in a single work cycle.
That’s how for example you can program the CNC center to perform flat grinding, drilling, and milling, and everything can be integrated into one program.
How CNC changed the metal industry?
Time is a very im0portant component in business. By applying the CNC machine metal processing , the time required to make individual positions is greatly reduced. In addition, CNC processing increases the processing speed, and repetitive processing requires a simple launch of the program.
On the other hand, classical processing without the use of the CNC technology requires a complete adjustment of both the tools and the machines during rework. In addition, by using the CNC technology, the size of a machine park is reduced but the quality of the end product is increased, and one machine can now be used to create a single position, while in the past several were needed.
However, with the obvious advantages of the CNC technology and CNC machining, there are some drawbacks as well. The disadvantages are linked to the high cost of such technology so only large and developed companies can obtain a CNC system.
Another disadvantage is the need for specific knowledge of employees related to programming knowledge.
What is the CNC technology applied for?
CNC technology can be used in various operations related to the processing of metals as well as other materials.
The most famous and most commonly used application of this kind of technology is turning or milling.
The CNC milling application in metal processing provides high precision and speed; which on the other hand is not provided by the conventional turning machine.Apart from that, the CNC technology is being applied during laser metal cutting, plasma cutting, water jet cutting, grinding, drilling etc.
In addition to its application in engineering or metallurgy, CNC technology is applied in a number of other industries. One example is the wood industry where the CNC is used for the same or similar purposes as with metal processing.